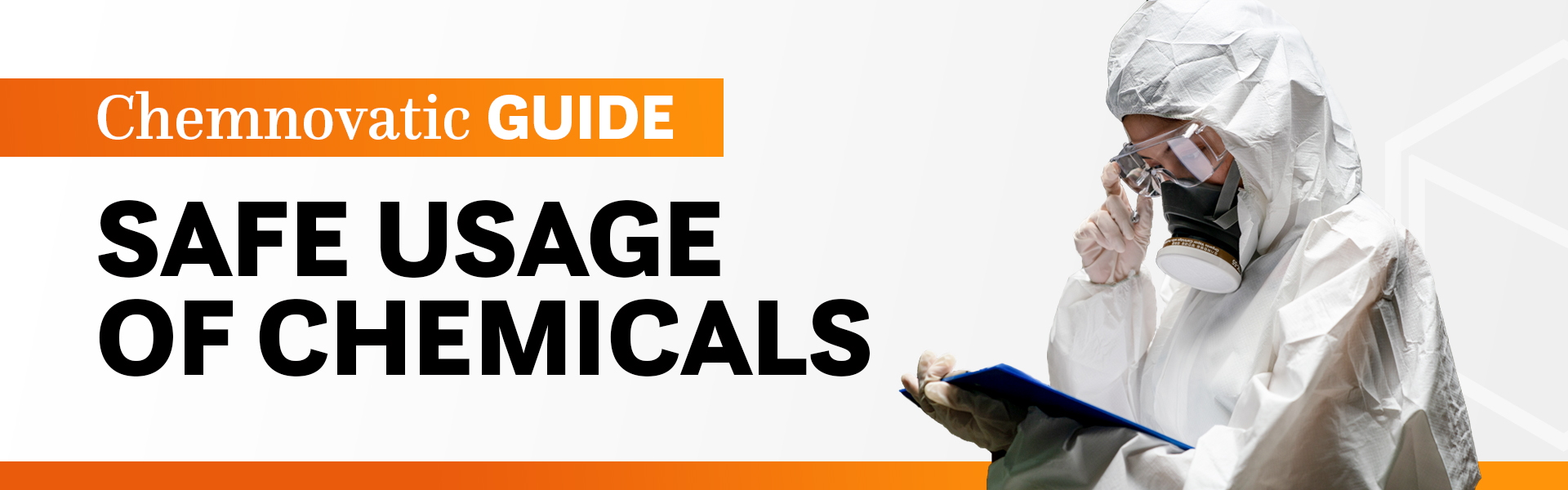
Safety is one of the key elements for the proper functioning of a company operating in the nicotine and chemical industries. In order to optimize processes, minimize risk and ensure the highest safety standards, Chemnovatic prepared a comprehensive guide “Safe Usage of Chemicals”. Thanks to this compendium, you will effectively minimize risks and ensure safety at every stage of production processes.
In this guide you will learn, among others:
- How to prepare for working with chemicals
- Legal bases and REACH registration
- Necessary tests and occupational risks
- Proper equipment and Terms of Use
- Adequate facilities and personal protective equipment
- Training Required
- How to read signs, pictograms and certificates
- What are signs and pictograms
- How to read and interpret signs and pictograms
- What are certificates, how to read them and why they are so important
- What is MSDS and how to read the documentation
- How to take care of employees and work safety in a production plant
- How to use chemicals safely
- How to safely transport and store chemicals
- How to prevent substances from entering the environment
In chemical and nicotine production, ensuring safety is a priority both for the health of employees, as well as for the functioning of the company and environmental protection. Safe practice is not only a legal obligation but also a moral responsibility. The introduction of high quality standards and safety requirements is the first step in building the foundation of an effective and ethical production.
The wide range of chemicals used in these industries carries both the potential to create innovative products and the risk of hazards. Therefore, proper understanding and adherence to safety standards is crucial.
Our guide is not only an introduction to the principles of safe handling of chemicals but also draws attention to the key procedures and guidelines which are necessary to achieve the highest safety standards in production processes.
It’s not just a set of tips; it is a clear step towards safer and more responsible chemical and nicotine production.
We encourage you to explore this important topic with us to create a risk-free working environment and a more accountable future for all of us.
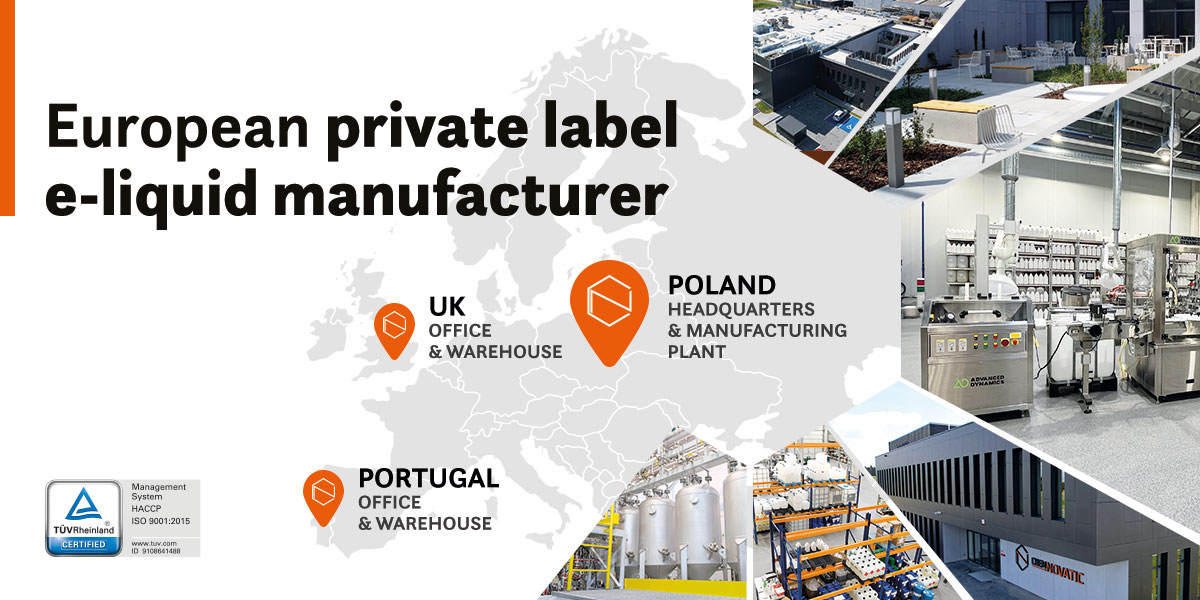
1. How to prepare for working with chemicals
Before entering the area of working with chemicals, it is crucial to understand the guidelines that will ensure safety and effectiveness in operation.
Here are the steps you should take care of before starting to work with chemicals:
- Notification of activity: Before starting work with chemical substances, it is necessary to report the activity performed to the relevant authorities to be able to act in accordance with applicable regulations. In the European Union, the rules for reporting your activities may differ from one Member State to another. The EU has a complex chemical regulation system, including REACH (Registration, Evaluation, Authorization and Restriction of Chemicals).
- REACH (Registration, Evaluation, Authorization and Restriction of Chemicals): Regulates the registration, evaluation, authorization and restriction of chemicals. Companies involved in the production, import, distribution or use of chemical substances in quantities exceeding certain thresholds may be required to register these substances with the European Chemicals Agency (ECHA). This registration includes the provision of detailed information on the properties, uses and safety of the substance.
It is worth emphasizing that these regulations are very complex and compliance with REACH requirements may vary depending on the type of substance and the amount in which they are used. Therefore, companies operating in the field of chemical substances in the EU should carefully read national and EU legislation on the registration and notification of chemical substances and cooperate with local regulatory authorities, such as chemical agencies, ministries responsible for environmental protection and public health. - Occupational Risk Assessment: Before working with chemicals, have an occupational risk assessment carried out. Such a process can be carried out internally by a team consisting of a person responsible for health and safety, the employer, management and, in selected cases, employees with the most extensive experience. This will help identify potential threats and determine the maximum permissible concentrations of harmful substances.
- Working Equipment: Make sure you have access to working machines, tools and equipment. Regular maintenance and proper operation are key factors for safe operation.
- Appropriate Rooms: Work in rooms that meet legal requirements, such as a minimum height of 3.3 m and 2 m² of free space per employee, unoccupied by devices and furniture or equipment. In addition, provide adequate mechanical ventilation to minimize exposure to harmful substances.
- Permits and Consents: Before starting your business, make sure you have all the permits required by law, for example for emissions or waste. Also ensure proper management of waste from hazardous materials in accordance with local regulations.
- Personal Protective Equipment: Provide and use necessary personal protective equipment (PPE), such as coveralls, gloves, goggles and masks. Each stage of working with chemicals (from production, through bottling and storage to transport) requires different protective measures. Follow the guidelines because your safety and that of your employees comes first. Please see section 4 for more information on PPE.
- Order and Ergonomics: Keep your workplace tidy to minimize the risk of unnecessary accidents. In addition, create an ergonomic workstation that will allow you to work effectively and safely.
- Employee training: It is extremely important to train the staff in the use of chemicals and safety rules. Make them aware of potential risks and proper practices. See Segment 4 for more information.
Remember that following the guidelines is the key to creating a safe and effective working environment in the area of working with chemicals. Acting responsibly will not only ensure safety, but will also have a positive impact on work performance.
2. How to read signs, pictograms and certificates
Signs and pictograms are graphic symbols that provide important information about chemical properties and potential hazards.
It is worth remembering that each chemical substance intended for professional use should be properly labeled. The lack of appropriate markings may indicate that the supplier has not met certain safety requirements.
In the nicotine and chemical industries, understanding these labels is essential to minimizing risks and implementing appropriate safety measures. Chemical labels are common and globally identical. This means that no matter what country you order a product or raw material from, the signs and symbols used have the same meaning.
Signs include:
- information about the name of the chemical,
- classification of the chemical,
- physicochemical properties of hazards that may occur during contact with a given substance.
In turn, pictograms:
- are graphical symbols that allow you to quickly recognize potential threats
- warn of the dangers of the substance.
There are two main standards for classifying pictograms: the Globally Unified System (GHS) and the ISO 7010 standard.
The GHS focuses on identifying the hazards of chemicals using various pictograms such as toxicity, flammability and explosiveness.
The ISO 7010 standard covers pictograms used in various areas, including evacuation, warning, prohibition and mandatory signs, which are intended to improve safety and understanding in workplaces, buildings and other environments.
All signs and pictograms are essential to ensure the safe use and storage of individual chemicals. People who work with them should be aware of potential hazards and take appropriate precautions to minimize the risk of dangerous situations.
Here’s a step-by-step guide to reading and interpreting this information effectively:
Step 1: Read the product label
On the package of the chemical or nicotine you will find a label with key information about the product. Pay attention to the name of the substance, its concentration, warnings and recommendations of the manufacturer or distributor for safe use.
Step 2: Understanding pictograms
Pictograms are graphical symbols that indicate the hazards of a chemical. Before using them, familiarize yourself with their meaning in order to consciously identify possible risks. The most important pictograms in the chemical industry, along with the explanation of their meanings, can be found above.
Step 3: Verify certificates
Make sure that the product has the necessary documentation and certificates, e.g. GMP (Good Manufacturing Practice) which is a certificate that the product has been manufactured in accordance with the best manufacturing practices. Verification of documents and certificates allows you to confirm the product’s compliance with the relevant standards and norms.
Step 4: Read the Material Safety Data Sheet (MSDS)
Material Safety Data Sheet (MSDS) is a document containing detailed information about a chemical, including its physical and chemical properties, safe use, possible health and environmental hazards, and procedures procedures in the event of exposure to the substance.
Step 5: Be aware of restrictions and recommendations
Familiarize yourself with the restrictions on the use of the chemical, especially if you are responsible for its production or storage. Pay attention to the recommendations for safe transport and storage of the substance.
If you intend to create your own mixtures, be sure to follow the recommendations regarding proportions and proper combination of chemicals. Your skills and knowledge have a huge impact on the quality and safety of the final product.
Step 6: Consult the experts
If you have any concerns or questions, please consult a health and safety or chemical management specialist. You can also contact the manufacturer or distributor for additional information.
Remember that the ability to read and interpret labels and pictograms is a key element in ensuring the safe use of chemicals, as well as in complying with relevant laws and regulatory standards.
In addition to the knowledge and ability to read pictograms and markings, it is also important to familiarize yourself with certificates. Certificates are extremely important documents in the chemical and nicotine industry, as they confirm the compliance of products with specific standards, norms and regulations. Valuable certificates are not only required by the relevant regulatory authorities, but are also an additional asset for companies that want to provide their customers with the highest quality and safety.
In the chemical and nicotine industry, we distinguish several key certificates:
- GMP (Good Manufacturing Practice) Certificate of Conformity – a certificate confirming that the company adheres to good manufacturing practice, which ensures high quality of products and safety for consumers.
- Quality Certificate ISO 9001 – is a certificate confirming that the company has a quality management system, which contributes to the continuous improvement of production processes and increasing customer confidence.
- HACCP Certificate (Hazard Analysis and Critical Control Points) – is a certificate confirming that the company has identified risks related to production and controls key points in the production process to minimize the risk of dangerous situations.
- RoHS (Restriction of Hazardous Substances) Certificate of Compliance – is a certificate confirming that the products meet the restrictions on the use of hazardous chemicals, which is especially important for companies in the electronics industry, but also in the nicotine industry, with products such as cartridges.
- CE (Conformité Européenne) is a mark that confirms the product’s compliance with European safety and quality standards. Indicates that the product meets the relevant health, safety and environmental requirements set out in the relevant European directives and regulations. The process of obtaining the CE certificate requires conducting appropriate tests, assessing compliance and meeting specific standards and requirements.
Certifications required in the chemical and nicotine industry are crucial to ensure compliance with regulations and standards, but it is also worth investing in quality certificates that increase the credibility of the company and build customer trust. The certificates confirm that the company operates in accordance with high standards, taking care of quality, safety and responsibility in its activities.
Also, you may check our quality standards here.
3. What is MSDS and how to read the documentation
MSDS (Material Safety Data Sheet) is a document containing detailed information about a given chemical.
It is an important source of information about the physical, chemical, toxicity, handling of exposure, and precautions to be taken when using the product.
In the case of chemical substances, the MSDS is of particular importance because it contains important information on the ingredients used in production, which can contribute to minimizing the potential risks arising from their use.
What to look for when reading the MSDS:
- Chemical composition and substance identification: Knowing the chemical composition allows you to recognize the substance content in a given chemical product and to detect the possible presence of hazardous substances. This will help ensure that when creating new mixtures, the raw materials are compatible with each other and do not react with unintended nipples.
- Physical and chemical properties: Knowledge of physical properties, such as boiling point and pH, allows proper storage and handling of the substance and the whole product.
- Health and environmental hazards: MSDS informs about possible hazards, such as toxicity or irritating effects of substances, which is important for occupational health and safety and employee health protection.
- Precautions: The dossier contains instructions on what to do in case of exposure to the substance, so that you can respond appropriately in emergency situations.
- Waste Disposal: Disposal and waste management information allows for proper disposal and recycling, which has a positive impact on the environment.
It is worth remembering that the MSDS should be available to all workers and users of chemicals to enable them to use the products appropriately and safely.
All Chemnovatic product MSDS files can be found here.
Following the recommendations and precautions in the MSDS helps minimize risks and ensure a safe work environment. At Chemnovatic, we make sure that all employees have access to relevant and constantly updated documentation and are aware of the need to comply with safety standards in our daily activities.
4. How to safely use chemicals?
The safe use of chemicals is a key element in ensuring employee health protection and minimizing the risk of potential accidents or failures. Here are some important tips for the safe handling of chemicals:
Provision of necessary protective equipment
A first aid kit, eye wash equipment, a safety shower (if required), and appropriate firefighting equipment appropriate to the type of hazard are essential. It is important to mark and access this equipment, as well as regularly train employees in its use in order to effectively respond to possible failures and threats.
Employee training
Training employees in the safe use of chemicals is an essential element of caring for their health and ensuring adequate knowledge of how to handle chemicals. Regular training will allow employees to update their knowledge and understand the latest safety standards.
Employee training should include recognition of potential hazards related to substances and preparations harmful to health and safety. For this purpose, attention should be paid to the labeling, which is based on CLP Directive (Classification, Labeling, and Packaging), which is the legal basis for the identification and classification of chemical substances. Familiarity with the labeling will enable workers to instantly understand the nature of the substance and its potential hazards.
Using appropriate personal protective equipment
Employees should be equipped with appropriate personal protective equipment, such as gloves, protective glasses, masks, or overalls, which will ensure protection against direct contact with chemical substances. It is also crucial to clarify that information on the use of PPE is included in the OHS system documentation, which serves as a guide and instruction for employees. This is where you’ll find guidance on when to use a particular type of glove or coverall to ensure the highest level of protection, depending on the characteristics of the substance and the activities anticipated.
During the various stages of contact with chemicals, it is important to use appropriate personal protective equipment to minimize potential risks:
- Transport and storage (risk of mechanical damage to containers): In this case, it is recommended to use appropriate work clothes and gloves
- Preparation of mixtures (risk of heat and splashes): The use of coveralls, tight goggles, a cap or hood and a P3 mask with ABEK absorbers is essential during this step. In addition, appropriate safety footwear is necessary.
- Confection: For protection, it is recommended to wear protective glasses, apron or protective clothing, protective footwear and class A gloves in accordance with EN 373.
- Labeling: During the labeling phase, it is important to use safety glasses, apron/protective clothing and safety shoes. Here too, class A gloves according to EN 373 are essential.
- Packing finished products: Appropriate work clothes and gloves are essential when packing finished products.
The introduction and use of the correct PPE during these key steps ensures worker safety and minimizes risks associated with chemical handling.
Health and Safety Instructions
Employee training should include discussion and understanding of health and safety instructions. These documents are key guidelines for what to do before, during, and in emergencies. Employees should be aware of how to react in different situations and how to minimize the risk of exposure to harmful substances.
Read the documentation
Before working with any chemical, it is essential to read the MSDS and other documents containing information about the substance. Understanding the chemical properties and hazards will help reduce risks, take appropriate precautions, and put in place procedures to ensure safety.
Storage of substances under appropriate conditions
Chemicals should be stored in properly labeled containers. Storage should take place under specific conditions, i.e. in places with appropriate temperature and humidity, away from other substances that may be reactive with each other. It is also advisable to include information on the label, such as the name of the substance, CAS number, production and expiry date, and hazards. Thanks to this data, employees can quickly and precisely identify the contents of the container.
Moreover, substances should be stored in a manner consistent with their characteristics and hazards. For example, flammable substances should be kept separate from oxidizing materials and toxic substances from food substances. Going one step further, substances should be properly separated and segregated in the warehouse or on the shelves. Ensuring that hazardous substances are separated from harmless ones avoids unintended reactions or contamination.
Appropriate use of facilities and equipment
Before starting work with chemical substances, employees should be properly trained in the operation and use of chemical devices and equipment.
Avoiding unsafe contact
Workers should be trained to avoid accidental exposure to chemicals, such as inhalation of fumes or ingestion. Do not eat any food or or drink liquids in the chemical work area. Wash and disinfect your hands frequently. In the event of an accident, appropriate safety procedures should be implemented immediately.
Disposal and recycling
Unnecessary or unused chemical raw materials should be properly disposed of in accordance with the regulations in force in a given country. In Poland, the Waste Act of 14 December 2012 is in force (Journal of Laws of 2013 item 21), which defines the principles of waste management. In the European Union, the Directive of the European Parliament and of the Council 2008/98/EC of 19 November 2008 on waste and repealing certain directives (OJ L 312 of 22.11.2008), which is the general framework of EU waste legislation. Recycling should be encouraged and promoted where possible to reduce environmental impact.
Implementing appropriate safety practices and procedures is essential to ensure the safe and responsible use of chemicals at our manufacturing facility.
At Chemnovatic, we make sure that all employees are properly trained and equipped with appropriate protective equipment, which allows us to minimize the risk of potential threats related to our activities.
5. How to take care of employees and the way they work in a production facility
The safety and well-being of employees is a priority in every production facility. Here are some key issues we take into account to take care of employees and ensure appropriate working conditions:
Health and Safety Training
Employees should receive regular health and safety training. These trainings should cover the principles of handling chemicals, using appropriate personal protective equipment, operating equipment and what to do in the event of a breakdown or accident.
Monitoring of working conditions
Providing the right working conditions, such as the right temperature, humidity and lighting, is crucial to the health and comfort of workers. Regular monitoring of these parameters allows for early detection of potential problems and appropriate response to them.
Workplace ergonomics
Designing workplaces in accordance with the principles of ergonomics helps prevent injuries and occupational diseases. Properly adapted furniture, tools and equipment allow employees to work in a comfortable and safe way.
Control of exposure to harmful substances
Workers exposed to hazardous chemicals should be regularly monitored for exposure. The adoption of appropriate procedures and rules of conduct (e.g. the use of ventilation and security systems, education and training of employees, personal protective equipment, monitoring the health of employees) allows you to reduce health risks.
In certain situations, it is also necessary to commission an accredited laboratory to conduct NDS (Exposure to Substances – they allow you to determine the levels of exposure of employees to given substances and compare them with the permissible occupational exposure values) and NDN (Exposure to Hazardous Agents – in addition, they include the assessment of environmental conditions and may lead to changes in work organization, adaptation of equipment or application of appropriate protective measures).
Based on these studies, employers can take specific actions to protect the health and safety of employees and minimize risks.
Following emergency procedures
The production facility should have developed emergency procedures in case of emergencies. Employees should be regularly trained in these procedures to know what to do in the event of an emergency.
Communication and support
It is important to maintain open communication with employees and encourage them to raise any concerns or comments regarding safety and working conditions. Providing support and responding to the needs of employees builds commitment and trust in the company.
Safety culture
The introduction of a safety culture that promotes responsible behavior and care for the health of employees is a key element in ensuring a safe and friendly working environment.
Ensuring safety and comfortable working conditions contribute to improving efficiency, reducing the risk of accidents and building a committed and motivated crew. Compliance with health and safety procedures and care for the well-being of employees allows the company to achieve lasting success and create a positive image on the market.
6. Safe transportation and storage of chemicals
In the factory safe transport and storage of chemicals play a key role in minimizing the risk of failures, accidents or exposure of employees to hazardous substances. Here are some important aspects for safely transporting and storing chemicals:
Labels and signs
Before starting the transport or storage of chemicals, it is necessary to accurately label the containers in accordance with applicable regulations. Labels should contain information about the name of the substance, its properties and hazards, and precautions.
Specialist containers
Chemicals should be stored in specially adapted containers that resist chemical reactions and prevent leakage. Such containers will be all marked according to the UN standard, which includes labels, pictograms and codes for hazards related to various types of chemical substances and hazardous materials.
The UN standard is intended to provide uniform hazard information to facilitate the safe transportation, storage and use of these materials around the world. Labeling according to this standard helps workers, carriers and others identify and respond appropriately to the hazards of hazardous substances.
Proper storage conditions
Storage of chemicals should be done under the right conditions, such as proper temperature, humidity and ventilation. Any substances that require special storage conditions should be stored in accordance with these guidelines and standards.
Separate storage
Chemicals should be stored separately from other substances that may be reactive with each other. Avoiding even accidental contact of different substances reduces the risk of a runaway chemical reaction.
Staff training
Employees responsible for the transport and storage of chemicals should be properly trained in safety rules and procedures for transport and storage.
Access only for authorized people
Access to stored chemicals should be restricted to authorized and properly trained personnel only. This will help reduce the risk of accidents, exposure and potential theft.
Emergency procedures
The production facility should have emergency procedures in place in the event of a spill, fire or other dangerous situation. Employees should be trained to deal with such situations.
Transportation in compliance with regulations
When transporting chemicals off-site, comply with applicable laws and requirements for the transport of hazardous materials. For land transport in Europe, the ADR agreement (Agreement concerning the International Carriage of Dangerous Goods by Road), which sets out standards for packaging, labeling and documentation. In the case of air transport, international IATA regulations (International Air Transport Association) impose specific requirements on carriers to guarantee safety during air transport.
All regulations and guidelines are aimed at minimizing the risk and protecting people, the environment and property during the movement of these substances.
Ensuring the safe transport and storage of chemicals is a key element in protecting health and the environment. Compliance with safety procedures and rules helps to minimize the risk of potential threats related to the transport and storage of chemical substances.
At Chemnovatic, we care about compliance with the highest standards in terms of transport and storage safety, which allows us to operate effectively, minimizing risk and ensuring the protection of our employees and the environment.
7. How to prevent substances from entering the environment
Care for the natural environment is one of the main priorities in Chemnovatic’s operations. Preventing the release of chemical substances into the environment is one of the key elements of our ESG strategy and social responsibility.
Here are some important principles and practices that should be followed in order to minimize the company’s negative impact on the environment:
Monitoring and reducing the emission of harmful substances
Constant monitoring of production processes helps to identify the most dangerous sources of emissions and places where chemical substances get into the atmosphere, water and soil. Thanks to this, it is possible to use modern technologies and solutions that will significantly reduce the amount of emitted substances.
Recycling and disposal
All waste and residues from production processes are subject to appropriate segregation, recycling or safe disposal in accordance with applicable regulations. The main goal is to reduce the amount of generated waste and make maximum use of available resources.
Responsible storage practices
Appropriate storage standards must be observed when storing chemicals. Appropriate storage rules include: separation and segregation of substances in order to avoid uncontrolled reactions between them, proper labeling, appropriate containers resistant to chemical reactions and leaks, and appropriate storage conditions (proper temperature and humidity). Preventing chemicals from entering the environment as a result of spills or uncontrolled reactions also plays an important role.
Employee education
Regularly inform employees about responsible handling of chemicals and caring for the environment. Organizing and encouraging active participation in training programs and ecological initiatives is a very important factor supporting environmental protection.
Cooperation with the local community
Establishing a dialogue with the local community is important to understand their needs and concerns related to the company’s operations. Constructive cooperation may include joint ecological, social and cultural initiatives or partnership with local entrepreneurs.
As Chemnovatic, among others we take an active part in the Council for Innovative Social and Economic Development of Lublin, under which projects for the benefit of the local economy are created.
Continuous improvement of the company’s functioning
An important element is the analysis of processes and practices in order to constantly strive to improve them in terms of environmental protection. In the case of potential threats, it is necessary to act proactively (education and training, security audits), as well as preventively and reactively (quick reaction, e.g. to a leak of a substance, should result from previously adopted procedures). At the same time, it is necessary to constantly monitor the current situation and draw practical conclusions for the future, thanks to which it will be possible to avoid similar situations.
Preventing the release of chemical substances into the environment is not only the company’s duty, but also an expression of concern for future generations and the condition of the planet.
At Chemnovatic, we take all possible measures to ensure that our activities comply with the principles of sustainable development. We minimize the impact on the natural environment and act with full social responsibility:
- we ensure compliance with ESG regulations and standards,
- we strive to effectively implement responsible business standards in the supply chain,
- we raise customers’ awareness of product quality,
- we limit the negative impact on the environment,
- we increase work safety,
- we are a team of qualified, responsible and ambitious employees whom we will be able to support in their development.
The Safe Usage of Chemicals: a summary
In the “Chemnovatic Guide – Safe usage of chemical substances” we discussed the key aspects related to safety, responsibility and sustainability in the nicotine industry and e-manufacturing -liquids.
Our goal is to ensure that all employees, business partners and stakeholders related to the company have access to relevant information and guidelines regarding the safe use of chemicals and nicotine.
In the guide, we addressed key aspects such as reading labels, pictograms, certificates and MSDS, as well as safe use of chemicals and nicotine. The introduction of appropriate training for employees, compliance with health and safety procedures and proper storage and transport of chemicals are extremely important to minimize the risk and ensure the highest level of safety in each production facility.
As part of our own business, we strive to continuously improve processes and procedures, while supporting responsibility and innovation. We believe that joint commitment to security and sustainable development contributes to building trust and loyalty of customers and partners, and also has a positive impact on our environment.
We encourage everyone to follow the guidelines contained in the “Chemnovatic Guide: Safe Usage of Chemicals” to jointly ensure safety in the workplace and, as a result, contribute to creating a better and more sustainable world, also for future generations.
For more useful information on production, safety and quality standards in the chemical, nicotine and e-liquid industries, read the following articles:
- E-Liquid & Vape Industry Regulations [Knowledge Base]
- Vaping Trends 2024: How Can They Help Grow Your Profitable Business?
- E-Liquids: Quality Standards And Practical Tips For Manufacturers
- E-Liquid Manufacturing Best Practices
- Storing And Handling Pure Nicotine And Nicotine Salts
- How To Work With Pure Nicotine Safely?
- Packaging, Transport And Storing: Why Are They So Important For Product Quality?
- E-Liquid Industry Regulations
- E-Liquid Regulations In The World
- 5 Steps To High Quality Nicotine Bases
- Tobacco Product Directive (TPD): All You Need To Know
- Pharmaceutical Quality Of E-Liquids: What You Should Know?
- What You Should Know About Harmful Substances In E-Liquid Flavorings?
- What Is UFI Code And How Does It Apply To The E-Liquid Industry
- What Is Reach?
- What Is CLP?
Let’s grow your business together!
Subscribe to our newsletter and receive a free access to our e-mail course on raw materials for e-liquids production (and more!).
No spam, only valuable content we promise to send you.
Ensuring safety in chemical and nicotine production is paramount for protecting employees, complying with regulations, and safeguarding the environment. Chemnovatic’s comprehensive guide on safe chemical usage provides vital insights and practices to achieve these goals effectively. It’s a crucial resource for promoting ethical production standards and minimizing risks across all stages of operations.
Thank you, ensuring employee safety, regulatory compliance, and environmental protection is our top priority. We’re glad you found our guide on safe chemical usage valuable. Your support encourages us to continue providing valuable insights and best practices. If you have any questions or suggestions, we’d love to hear them!
This comprehensive guide, “Safe Usage of Chemicals,” by Chemnovatic is essential for anyone in the nicotine and chemical industries. It covers preparation, legal requirements, safety equipment, and more, ensuring top safety standards and responsible production practices.
Thank you for your comment. You can find more information at our Knowledge Base! :) We appreciate your support!